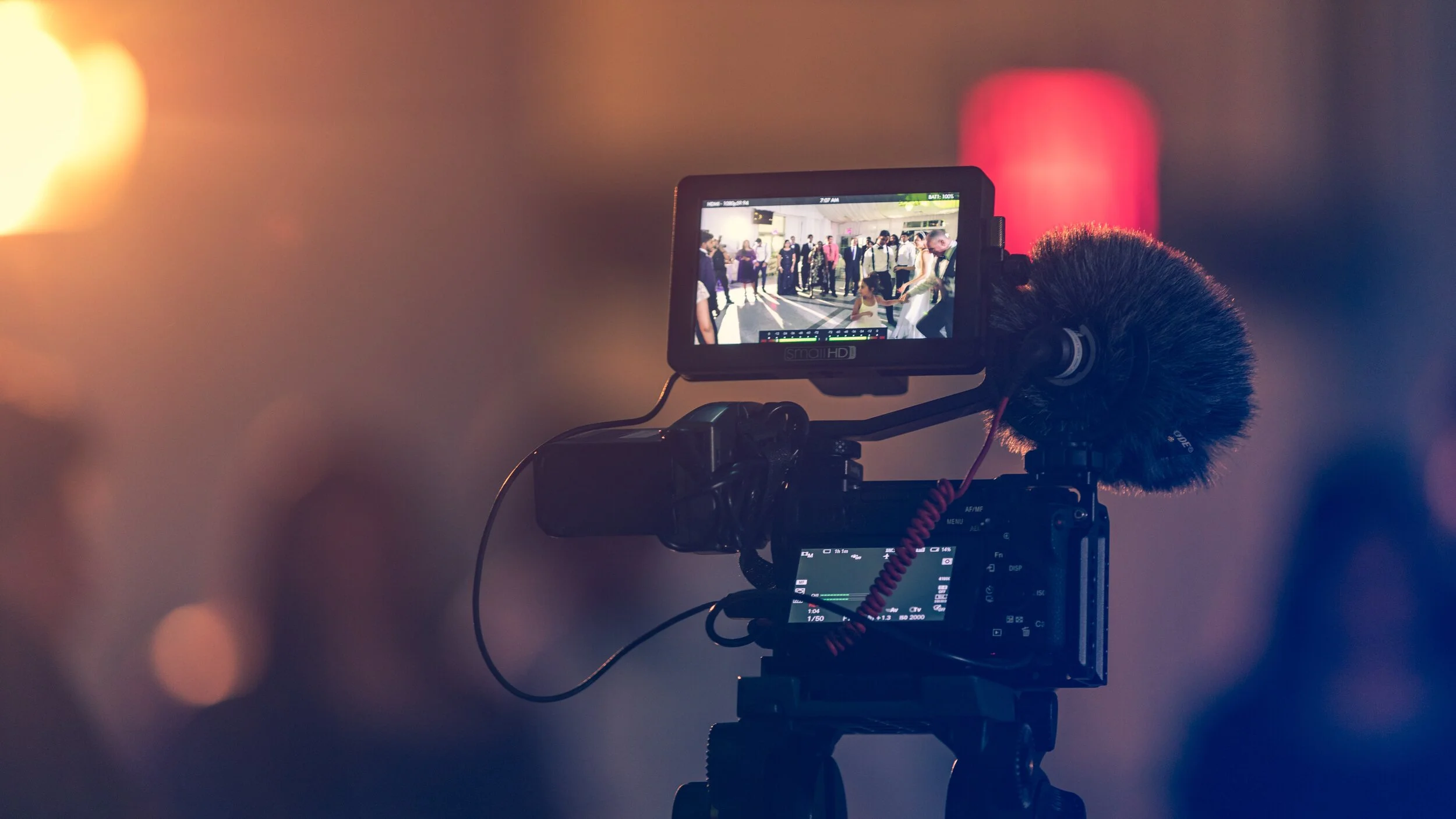
Production Departments and Work Practices
For all work practices canvassed in this section, the following approach is taken:
Identify hazards—find out what could cause harm
Eliminate risks so far as is reasonably practicable
Implement control measures for risks that cannot be eliminated
Communicate with all production employees about the type and scale of activity that may affect them
Plan for emergencies
+ Art department / construction
GOLDEN RULES
- Identify prop, construction, and demolition challenges in pre-production.
- Develop a clear schedule of works.
- Provide for risk elimination and mitigation in the planning stages.
- Appoint a Location Manager.
- Engage a Construction Supervisor and use only qualified/competent production staff.
- • Consult all key PCBUs as plans evolve.
PCBUS
Producer, Art Director, Production Designer, Set Designer, Construction Supervisor, Safety Supervisor
The Production Designer and Art Director should start their analysis of safety and work programmes when they receive the script and final schedule. They must:
- work closely with the location manager so they aware of when locations can be prepared;
- work closely with the construction supervisor and HODs during the design phase to ensure safe construction methods are incorporated;
- consult, cooperate and coordinate with the gaffer/head electrician; and
- consult, cooperate and coordinate with the cinematographer, special effects supervisor, visual effects supervisor and key grip.
PRE-PRODUCTION
Before the production starts, the producer should ensure:
- in consultation with the production designer/art director, that a competent construction supervisor, with suitable experience for the size of the project, is hired;
- a health and safety supervisor has been appointed (otherwise, the Construction Supervisor will be responsible for construction-related work health and safety);
- consult, cooperate and coordinate with the construction supervisor to determine the amount of work required and how long it will take, and take this into account when developing schedules;
- ensure hazard identification and risk assessments are undertaken for construction work; and
- ensure all potential risks on location are eliminated or, if elimination is not reasonably practicable, minimised and controlled.
The risk assessment process will:
- set out risks to members of the production team, artists, crew, other contractors, contributors, and other parties; and
- identify appropriate control measures for any sets or scenery, including props.
SET CONSTRUCTION
When a film set is under construction (or being dismantled, known as striking) it is no different to any other construction site. This means that the recognised PCBU must establish processes to:
- control and/or secure site access;
- identify and protect electricity and other services;
- implement work control measures to safely manage risk – e.g., working at heights, excavation;
- manage workloads; and
- provide for first aid and emergency responses.
SET CONSTRUCTION PERSONNEL
Everyone involved with the construction department:
- must be competent to undertake their assigned work, including being licensed, certified, or ticketed where required;
- must have the ability to identify that the equipment that they are using is safe and be able to maintain that equipment;
- should be aware of what personal protective equipment (PPE) is required and who will provide it; and
- should attend department-specific health and safety toolbox meetings, if required by the construction supervisor
- must be aware of those working around them.
+ Cameras / lighting
GOLDEN RULES
- All electrical work to be performed by qualified electrician.
- Rigging to be done by experienced rigger.
- Check for overhead obstruction and risks.
- Secure all mobile objects.
- Ensure stable and sure surfaces for cameras and related equipment.
PCBUS
Producer, Director of Photography and Grip, Gaffer / Head Electrician, Best Boy
CONTROL MEASURES
PCBUs should ensure, so far as is REASONABLY PRACTICABLE, that production personnel are not exposed to risks to their health and safety. Where risks cannot be eliminated, control measures must be implemented. Control measures should be discussed with the production personnel involved.
CAMERA CRANES
The Assistant director should ensure that the use of a camera crane is noted in the call sheet.
Grip equipment is generally very heavy and requires careful handling and skill. The resources required to lift and piece together equipment is easily underestimated. Wherever feasible, the use of mechanical lifting equipment is recommended.
In all circumstances, provide for a minimum number of crew for moving and ongoing supervision of the rig, irrespective of whether it is in use.
An experienced and competent key grip should supervise the setting up and operation of all camera equipment.
The main tasks of anyone supervising the set-up and operation of camera equipment such as cranes/jib arms is to:
- Observe safe working loads;
- Cables should be serviceable and kept away from the wheels when the dolly is moving;
- Check for overhead obstruction(s);
- Ensure the crane and camera are balanced;
- Ensure the arc of the camera’s field of operation is clear or protected;
- All parts of the crane should be kept clear of any non-insulated electrical equipment;
- When used on a public thoroughfare, adequate signage and barricades should be used to ensure safe operation of the crane;
- Cranes should not be operated on sloping ground or unstable surfaces;
- A riser used in conjunction with a camera crane should be able to support the aggregate weight of the crane, any personnel using it, and any additional loads; and
- The riser should also be braced and/or constructed in such a way as to prevent collapse.
In erecting, using and dismantling equipment, clear communications protocols will be required. There should be a nominated ‘person in charge’ (ordinarily the key grip) that is known to all.
The camera equipment’s operating area (or ‘arc’) should be kept well clear of non-essential personnel, any other person not specifically required, and any equipment not required for the filming.
Where cast or crew are required to move under a crane or jib arm, they should do so on the instruction of the Key Grip or Senior Camera Operator.
MOTION CONTROL CAMERAS
In addition to the guidance above, the safety steps for motion control cameras include:
- Camera start and finish positions shall be clearly marked and, where possible, barriers established;
- An assistant should walk the camera head through the range of movement to ensure the pathway is kept clear prior to block through, rehearsals and filming;
- Crew and performers should be fully briefed on the operation of the motion control camera and related safety requirements the pathway the equipment will be following and the need for crew and performers to always remain clear of the track;
- When the motion control camera commences operation, the operator shall call “rig moving”;
- Only essential personnel shall be on set during sequences involving motion control filming; and
- All motion capture cameras should be run on a separate power supply and the Gaffer should be consulted regarding power requirements, power distribution and power safety.
LIGHTING
Most of the safety guidance relevant to lighting is included in the Electrical Work note in section EB4. Please review the content of this note. The general rules for safe handling of lighting are:
- Specialist lighting – and the replacement of lamps - should only be handled by trained personnel;
- Ensure that all lighting fixtures are supported so that they will not fall, i.e., use a safety wire or chain to suspend fixtures. Consider multiple points of possible failure;
- Ensure that all lighting stands are property weighted with sandbags or fixed to the ground;
- Use fall protection equipment whenever setting up lighting at elevated heights;
- Cover arc-type lamps such as HMIs in wet weather to prevent rain from entering the unit;
- When using open-faced lighting units, provide protection from shrapnel in case the bulb explodes; and
- Ensure that scaffolds or other metal grids that are used to support the lighting are grounded.
+ Makeup, hair and wardrobe
GOLDEN RULES
- Makeup artists should be the only people responsible for the application and removal of makeup.
- Only use ingredients-labelled cosmetics and hair products from established and reputable manufacturers.
- Fit for purpose workspaces must be provided – i.e., well-lit, ventilated, and hot and cold running water.
- Any possible health risk arising from the use of particular substances should be relayed to performers receiving hair, make-up, and wardrobe services.
- Maintain high levels of hygiene and effective cleaning protocols.
PCBUS
Producer, Heads of Make-up, Hair and Wardrobe and subordinate Artists. (Safety Supervisor and/or Stunt Coordinator where SFX used.)
PRODUCER / PRODUCTION MANAGER
The producer / production manager should consider hair, make-up, and wardrobe resources in pre-production; this includes:
- hiring competent hair and make-up artists with an appropriate level of training, experience and/or qualifications with respect to the requirements of the production;
- the number of hair and make-up artists hired in relation to the size of the project;
- ensuring sufficient resources, including budget, are allocated to enable the use of appropriate and safe products such as single use implements and products; and
- ensuring guidelines on hazardous chemicals (and fire) are adhered to.
HEADS OF DEPARTMENT
The chief make-up artist, hair stylist or head of wardrobe should ensure that they and those working under them are familiar with these guidelines and best practice health and safety.
RESPONSIBILITIES SPECIFIC TO HAIR AND MAKE-UP
Hair and make-up artists are to:
- be fully proficient in the knowledge of products, procedures, and techniques to be carried out when performing their role;
- check that electrical equipment has been tested and tagged;
- be informed of the possible risks and side-effects of certain hairdressing or makeup products;
- where possible, undertake make-up or skin tests to ascertain if a reaction is likely to occur;
- check with the cast regarding allergies or sensitivities to certain products;6
- follow general hygiene rules such as washing hands before and after each hair or makeup application;
- consider single-use lipsticks, mascara wands, puffs, and sponges where possible;
- where single use products are not available or feasible, disinfect application equipment when moving from one artist to the next;
- when applying dye or colouring or when perming or straightening hair, appropriate gloves must be worn, and the ventilation must be adequate;
- as much as possible, avoid using sprays; otherwise, avoid being in the spray cone, limit the time of use, and use a face shield to protect the cast member;
- keep products at the proper temperature, and ensure flammable liquids and aerosols are kept in a cool place, away from sources of heat and flame. (The manufacturer’s recommendations about the product’s use and storage must be followed);
- controlled substances decanted from the original container into another container must be labelled and an inventory of their use maintained;
- preferably use products in gel or cream form and avoid powders that must be mixed; and
- use a disinfected spatula to remove a product from its container (do not use fingers).
HYGIENE
Makeup Artists and Hairdressers should maintain a high standard of hygiene with the minimum use of hand/wrist jewellery. This includes thorough hand washing between use of products and changes in the personnel being provided makeup.
Cuts and abrasions on a make-up artist’s exposed skin should be covered by a waterproof dressing which should be changed as necessary and when soiled.
Equipment and accessories used for various treatments should be cleaned and disinfected with an alcohol isopropyl product (of at least 70% purity) after each use, and then stored in a clean location, protected from dust and dirt.
Each cast member should have their own sponges, powder boxes, combs, and brushes.
WORKSPACES
The working environments in which hair, make-up and wardrobe duties take place must be:
- clean, well-maintained (i.e., regularly disinfected) and have adequate ventilation;
- smoking, eating, and drinking should not be permitted;
- aerosols should not be used in small unventilated spaces dressing rooms / facilities;
- changing facilities should be adequate and have regard to privacy and the design and dimensions of costumes, wigs, and makeup;
- have adequate lighting inside and outside;
- have hot and cold running water, with clean water available to rinse eyes from contact with hazardous substances
- the floor should be unobstructed, swept regularly and kept clean to avoid falls; and
- facilities should have height-adjustable chairs, an anti-fatigue mat (rubber mat that absorbs impacts), first aid kit, fire extinguisher and an eye clean station.
MOBILE VEHICLES WORKSPACES
- If a vehicle is provided as the hair and make-up workspace, the vehicle should be level, stable, comfortable and, wherever possible, have access to hot and cold running water.
- Trailers or caravans should be checked, preferably by the person hiring the vehicle, to ensure that:
- all the correct certificates, including insurance, gas safety and electrical appliances, are valid and current;
- all drivers have a current valid license; and
- the vehicle is capable of being plugged into mains power and has a current Electrical Warrant of Fitness.
SPECIAL EFFECTS MAKE-UP
Special attention should be given to the needs of actors who are required to keep prosthetic or special effects makeup on for lengthy periods or during tea and meal breaks. Adequate air conditioning and/or heating, appropriate cool rest areas, straws, appropriate diet, and other relevant assistance should be provided.
Where a performer is required to wear extensive prosthetics such as a full head or full body prosthetic or creature suit, consideration should also be given to balance, stress, strain and/or exhaustion that might cause by heat, vision impairment, restricted mobility and/or isolation.
Care should be taken when body suits are used in wet environments as such suits may absorb liquid and become severely weighted causing difficulties including the risk of fatigue or drowning.
Where special effects makeup involves the use of hydraulics or air-pressurised equipment, consideration should be given to the impact discharges might have around the eye area or other areas of the performer’s body.
Special effects makeup should be removed with non-solvent materials, such as isopropyl myristate.
Makeup should never be used on babies aged under twelve weeks.
The design and manufacture of all costumes, wigs and prosthetic and special effects makeup should take account of the possibility of heat exhaustion and hyperthermia and be designed to accommodate the performer’s natural functions, including eating, drinking, and going to the toilet at adequate intervals.
Use of products on animals for the purpose of cosmetic enhancement or causality simulation shall be undertaken in consultation with the animal handler and all products used should be non-toxic and in accordance with relevant legal standards and codes of practice covering animal welfare and their use in film production.
WARDROBE
The Producer should notify the Costume Designer of all sequences involving the use of:
- flame, flash effects, where the possibility of fire exists;
- all sequences involving stunts; and
- all sequences involving blue screen work and/or scenes requiring performers to work in or with rigs to ensure that all costumes can be designed and manufactured in a manner that ensures the safety and comfort of performers.
The costume designer or person with delegated responsibility should consult with the stunt coordinator and special effects supervisor prior to designing wardrobe for use in fire sequences.
Designers should be advised of performance requirements to ensure that the design of masks, headwear and special effects and prosthetic makeup does not restrict the performer’s vision.
The Costume Designer should be given adequate time to work with the Special Effects and/or Stunt Coordinator and Designer to ensure that potential risks are minimised or eliminated.
GENERAL RULES FOR COSTUME
- Wigs and costume fabrics should be non-synthetic for use in scenes involving fire or a naked flame.
- Retardants should be used whenever practicable, subject to an assessment of possible skin irritation.
- Cast wardrobe and footwear should be designed to suit the scenes/action to be shot.
- Each performer should be provided with dedicated costumes including shoes and wigs to reduce the likelihood of infection.
- It is the producing company’s responsibility to maintain and launder costumes.
- For any stunt, special effect, or hazardous action the wardrobe department should liaise with the Safety Supervisor and/or Stunt Coordinator for appropriate materials, length of garment, footwear etc.
- Costumes and wigs to be used in potentially hazardous sequences (e.g., fire, explosives, bikes, cars, performing with animals, etc.) should be designed, treated, and manufactured in such a way as to reduce the risk of injury.
USE OF DYES
- Use of internationally recognised Colour Index (CI) assists in identifying dyes.
- MSDSs should be obtained for all dye products being used.
- Care should be taken to avoid inhaling or ingesting dyes or making skin contact with dyes.
- Protective clothing goggles and gloves should be worn when handling dye products.
- Wherever possible, it is preferable to use liquid dyes rather than powders to minimise the chances of inhalation.
- Water-based solutions are safer than solvent-based solutions which use methyl alcohol.
FABRICS
When choosing fabrics, consideration should be given to:
- the climate in which the production is being shot, its impact on artists and remedial measures to ensure the welfare of the costume wearer;
- the flammability potential of any fabric to be used in a scene involving flames, excessive heat, the potential for flames, proximity to heat sources including lights, etc.; and
- the possibility of skin irritations caused by the fabric/s, for instance and the potential need for substitute materials.
+ Catering
GOLDEN RULES
- Facilities (mobile or fixed) must be fit-for-purpose and certified by the relevant State/Territory Health or Food Safety authority.
- Catering equipment to be fitted with guards where appropriate.
- Staff to be trained in equipment usage and associated risks.
- Develop systems for identifying allergen and other risks in the provision of food.
- All relevant staff to be trained in safe food preparation and storage protocols.
PCBU
As with the majority of film production operations, the Producer bears overall responsibility for ensuring that services provided to cast and crew are of a reasonable and safe standard.
With respect to catering, this duty includes taking reasonable steps to:
- provide suitable food and sustenance and managing the timing for the delivery of these services during production;
- ensuring the provider of catering services is competent to discharge the relevant duties; and
- allocate sufficient space for the provision of all catering services for the safe conduct and delivery of catering operations.
CATERING SERVICE PROVIDER - EMPLOYER
Filming on location commonly involves the use of a mobile catering resources, normally trucks and vans specifically equipped to provide food and beverage services. This section focuses on these (mobile) resources.
It is the responsibility of the head of the catering entity (nominally the head catering contractor to a production) to ensure that catering services are delivered in a safe and responsible manner. There are three key parts to this responsibility:
- ensuring the safety and utility of mobile catering units;
- ensuring the quality and safety of the consumables being provided to cast and crew; and
- taking all necessary steps to ensure the safety of the staff delivering the catering services
Any person undertaking a food business must also:
- ensure food handlers do not handle food if there is a risk of contamination;
- maintain easily accessible handwashing facilities, with hot water, soap, and single-use towels; and
- ensure all food handlers have reasonable and appropriate training in food safety and food hygiene.
SAFETY OF FOOD AND DRINK
Persons supervising or conducting food handling operations must possess the skills and knowledge in food safety and hygiene matters required to handle food safely. This will involve knowledge of food handling and safety procedures, including knowledge of the risks that certain conditions (e.g., humidity, heat and light) might pose to food safety and the corresponding need to ensure the proper storage (i.e. temperature-controlled) of foodstuffs.
Federal, State and Territory governments have produced a wealth of statutory requirements applying to the provision of food and beverage services. The essence of these requirements (drawn mainly from Food Standards Codes) is:
- catering staff should be suitably trained and qualified to perform the task(s) they are required to perform, including the ability to properly sanitize plates/utensils, etc.; and
- catering staff must take all reasonable measures not to handle food or food surfaces in a way that is likely to compromise the safety and suitability of food.
Catering staff also have specific responsibilities relating to health and hygiene.
Health responsibilities include not performing work when they have symptoms or a diagnosis of conditions such as diarrhoea, fever and/or vomiting.
Hygiene responsibilities include not coughing, sneezing, or smoking around food of food production surfaces. In addition, food prep and delivery staff should take steps to remove unnecessary jewellery, and contain long hair, cover small wounds (i.e., scratches) with bandages etc and a waterproof covering.
SAFETY OF CATERING STAFF AND USERS
Food preparation and other catering workers should:
- Be trained to use equipment properly, including the safe use of knives;
- Be supervised when first using machines;
- Be provided with sufficient space to perform their duties; and
- Always be provided with and wear the right personal protective equipment and clothing (gloves, glasses, apron, footwear).
To ensure worker safety:
- Guards should always be attached when using machines to protect from moving parts. Only remove them for maintenance;
- Machines on work tops should be level and bolted down so they do not move when used;
- Where possible, rotate people through tasks to allow changes in posture and activities. Avoid doing the same repetitive tasks over and over when working over long periods;
- Breaks should be taken to avoid fatigue (and/or as required under employment agreements);
- Ensure that protocols for handling hot oil and its disposal are safe and known to relevant staff;
- All relevant catering staff should be provided with fire suppression and extinguishment resources and the knowledge of how to use them when required;
- Mechanical aids should be used where possible (e.g., food mixers/processors, peeling machines); and
- Catering tools such as knives should be maintained (i.e., sharpened) to avoid forceful movements.
CATERING VEHICLES / UNITS
General considerations for catering vehicles include:
- The vehicle/s should be roadworthy, registered and in a serviceable condition;
- Relevant Food Regulator/Department of Health certificates should be displayed or otherwise available for production;
- The vehicle/s should be appropriately fitted out in accordance with relevant electrical and gas Safety Guidelines, well-maintained, well-lit, and kept in a hygienic condition;
- The vehicle should be levelled and parked safely;
- Safe entry and exit should be provided and, where necessary, steps should be safe, and have handrails fitted;
- Fittings and fixtures should be serviceable and appropriate;
- Machinery and equipment that can cause injury is to be suitably guarded;
- All electrical equipment should be serviceable, tested and tagged;
- All gas equipment should be serviceable and comply with relevant Australian Standards;
- Emergency gas and electricity shut-off should be provided for;
- If external power is required, the vehicle should be supplied with the correct leads for that particular vehicle;
- Power cords should be protected to prevent tripping;
- Suitable and sufficient fresh and wastewater capacity is available;
- Fire extinguishers should be in good working order and in current test, tagged and logged;
- Employees working from the vehicle should be appropriately trained to handle food and use the equipment in the vehicle;
- Adequate headroom should be available;
- Sufficient cold storage for foodstuffs for the numbers being catered; and
- Heating equipment such as Hot Water Urns should be positioned safely, and measures implemented to minimise the risk of burns.
MARQUEES/TENTS
Care should be taken when siting marquees and tents and consideration given to the following:
- Marquees/tents should be in good condition and fit for the purpose;
- Erect marquees/tents on firm, non-muddy ground;
- Free standing or framed marquees/tents should be adequately secured;
- If using pegs, establish if there is underground power, water, gas, telephone in the vicinity;
- Tie lines and pegs can be a major trip hazard, ensure they are well marked/fenced off/safe walkways established, etc.;
- Check for overhead power lines and overhanging tree branches;
- Adequate walkways should be considered and if necessary temporary walkways installed;
- Appropriate measures should be taken to avoid the risk of fire from heaters and/or lights; and
- Lighting in and around marquees/tents should be appropriate.
+ Working at heights
Falls from heights are a major cause of fatalities and serious injuries. Most people who are seriously injured or killed, fall from a height of four metres or less.
PCBU
A PCBU must eliminate the risk of falls in the workplace, or if that is not reasonably practicable, minimise those risks so far as is reasonably practicable.
Generally speaking, tasks at heights under 2 metres require safe work procedures to be developed and implemented to minimise the risk. Tasks performed above 2 metres are considered high risk and require a safe work method statement (SWMS).
It is critical to note that a minimum clearance of 4 metres should be maintained between mechanical equipment and overhead electric power lines.
(Greater separation clearances may be specified in Australian Standard (AS) 1418 – Cranes, Hoists and Winches - in certain circumstances.)
Due to the inherent risk of injury or death, it is important to speak with everyone involved in working at heights. They may have experiences and views that are critical to work being carried out safely.
SCAFFOLDS
Scaffolds can be very effective protection in preventing falls, but they are not without risk.
Safety considerations when using scaffolds should include:
- Scaffolding conforms to AS/NZS 4576:1995: Guidelines for scaffolding and the AS/NZS 1576 Scaffolding (set);7
- Fall prevention and arrest equipment is used;
- Scaffolding is erected, altered, and dismantled by competent people;
- Safe access to and exit from the scaffold is provided; and
- Edge protection like handrails, mid-rails and toe-boards is provided at every open edge of a work platform.
If the potential fall distance from a scaffold is less than two metres, it may be erected or dismantled only by a competent person who has trained in respect of the type of scaffolding being used.
If the potential fall distance is greater than two metres, scaffolding should be erected or dismantled only by a holder of a certificate of competency for that class of scaffolding or a person under the direct supervision of a person with the correct certification.
Scaffolding work platforms are generally rated as light, medium or heavy duty:
- Light duty—up to 225 kg per bay. Examples include painting, electrical work, many carpentry tasks, and other light tasks. Platforms should be at least two planks wide (approximately 450 mm).
- Medium duty—up to 450 kg per bay. This is suitable for general trades work. Platforms should be at least four planks wide (approximately 900 mm).
- Heavy duty—up to 675 kg per bay. This is what is needed for bricklaying, concreting, demolition work and most other work tasks involving heavy loads or heavy impact forces. Platforms should be at least five planks wide (approximately 1000 mm).
- Special duty—has a designated allowable load as designed.
These safe load limits include the weight of people plus the weight of any materials, tools, and debris on the working platform.
Safe construction methods should be used for scaffolds, including:
- Ensure only correct materials for the load are used in accordance with AS 1576;
- Inspect all equipment and materials before use, and repair or dispose of any rejects;
- Tie scaffold effectively, both longitudinally and transversely, with safe means of access and egress;
- Fully plank out scaffolding more than 1.8 metres high, with properly supported planks of the correct size, toe boards and continuous handrails to ensure a safe work platform; and
- Mobile/wheeled scaffolding should not be moved whilst supporting people, and all wheels should be locked before anyone works on it.
CONTROL MEASURES
Control measures include the provision of information, training, and instruction to workers prior to undertaking work from a scaffold. The PCBU and workers should know what loads the scaffold can safely take (Safe Working Load (SWL)) and under no circumstances make unauthorised alterations to a competently erected scaffold.
Scaffolding must:
- be level and plumb;
- be clear of debris and obstructions along their length;
- accessed using an internal ladder, except for low height platforms where this is not reasonably practicable;
- where there are no guardrails, use an approved safety harness connected to a secure anchor point;
- workers must wear appropriate, non-slip footwear; and
- electrical leads must be isolated from the metal frame of the scaffold with plastic lead hooks or an insulated rubber material where reasonably practicable (to prevent damage to the leads or electrifying the scaffold).
Workers on scaffolds must not:
- work beyond the side of ladders or over guardrails; or
- place ladders on other structures to extend their reach.
Appropriate precautions should also be taken against injury to people below those working at a height, including:
- take aloft only essential tools and equipment;
- prior to ascending, secure all tools and equipment with lanyards to prevent them falling on those below, and empty pockets of any unsecured items; and
- implement appropriate control measures to prevent props, sets, equipment, including cameras, etc. from creating a risk by falling.
In addition, height rescue procedures should be developed for each workplace where working at heights is undertaken.
FALL-PREVENTION AND ARREST
A risk assessment should be undertaken to determine the most appropriate form of personal fall protection equipment for the situation – refer AS1891 – including:
- travel restriction devices are to be preferred to fall arrest devices;
- anchorage points should be capable of sustaining the load of the person falling;
- all persons who need to use fall protection equipment should be trained in its use and maintenance; and
- adequate supervision should be provided to people using fall protection equipment.
A fall-prevention device is best because it will prevent workers from falling. Examples include temporary work platforms, guardrails, and scaffolding.
When it's not possible to use a fall-prevention device, a work-positioning system or a fall-arrest system should be used. A fall-arrest system is generally a harness worn by the worker to stop a person who has fallen and reduces the impact of the fall.
All harnesses, lanyards, fall arrest and fall restraint devices should be manufactured and maintained to Australian Standards.
No person shall be allowed to undertake work requiring the use of fall restraint or fall arrest devices without having undertaken appropriate training in the use and maintenance of such devices.
An effective communications system between those at a height and those on the ground should also be implemented.
LADDERS
Falls from ladders have resulted in a significant number of serious and fatal injuries, even when working at relatively low heights. While ladders are often considered to be the first option when working at heights, they should only be considered after safer alternatives, for example elevating work platforms (EWPs) or scaffolding, have been considered first and found to be not reasonably practicable.
Extension or single ladders should only be used as a means of access to or exit from a work area or for short duration light work that can be carried out safely from the ladder. Ladders should have a load rating of at least 120 kg and be manufactured for industrial use. Domestic or ‘homemade’ ladders should not be used.
RISK ASSESSMENT AND CONTROL MEASURES
Before setting up a ladder, it should be inspected for visible damage or faults, for example broken rungs, stiles, and footings. Faulty or damaged ladders must be removed from service.
When setting up a ladder you should check that:
- the ladder is the correct height for the work to avoid over-reaching or stretching;
- locking devices on the ladder are secure;
- the ladder is not placed so that the weight of the ladder and any person using the ladder is supported by the rungs;
- ensuring the ladder has non-slip feet;
- placing ladders at a slope of 4:1 (the distance between the ladder base and the supporting structure should be about 1 metre for every 4 metres of working ladder height);
- securing ladders at the top or bottom, or if necessary, at both ends; and
- stepladders should be set up in the fully opened position and may require a second person to ‘foot’ the ladder for added stability.
When using a ladder, always maintain ‘three points of contact’ as follows:
- when going up or down a ladder, always have two feet and one hand, or one foot and two hands, on the ladder; and
- when working from a ladder, have two feet and one other point of contact with the ladder, such as a hand or thighs leaning against the ladder.
Do not:
- use metal or metal reinforced ladders when working on or near live electrical installations;
- carry out ‘hot’ work like arc welding or oxy cutting from a ladder;
- use power or hand tools requiring two hands to operate, for example concrete cutting saws and circular saws;
- use tools that require a high degree of leverage force which, if released, may cause the user to over-balance, or fall from the ladder, for example stillsons or pinch bars;
- over-reach—the centre of the torso should be within the ladder stiles throughout the work;
- face away from the ladder when going up or down, or when working from it;
- stand on a rung closer than 900 mm to the top of a single or extension ladder;
- stand higher than the second tread below the top plate of a stepladder except for three-rung stepladders, unless working through an overhead opening of the building or structure that provides appropriate additional support above the ladder;
- in very wet or windy conditions; or
- next to traffic areas unless the working area is barricaded.
PLATFORMS SUPPORTED BY TRESTLE LADDERS
Trestle scaffolds are generally not suitable for working at heights of 2 metres or above. If they are used at heights greater than 2 metres, guardrailing and toe-boards should be used to prevent people and material from falling off the open side or end of the work platform.
Working platforms on trestle scaffolds should have a width of at least 450 mm (two planks). The use of plank locking devices will extend plank spans and reduce plank whip when walking along the platform. The system (including planks) should be assembled according to the manufacturer’s specifications using only compatible components.
A PCBU must always consider what is reasonably practicable to maintain a safe system of work in the circumstances. It may be that a trestle scaffold is not the most appropriate means of minimising the risk of a fall in the circumstances. Therefore, alternative types of temporary work platforms should be considered, for example EWPs like small scissor lifts and other types of fall prevention devices like light duty aluminium mobile scaffolds and modular scaffolding.
ELEVATING WORK PLATFORMS (EWPS)
EWPs include boom-type EWPs and scissor lifts. Some are designed for hard flat surfaces only while others are designed to be operated on rough terrain. Some types are designed for indoor use and are not suitable for windy conditions outdoors.
The key steps for EWP use are:
- only operators competent in the use of the equipment may use it and should, as specified in relevant jurisdictions, hold appropriate certification; and
- use equipment in accordance with the manufacturer’s specifications.
RISK ASSESSMENT
If using an EWP at the workplace, the PCBU and relevant workers must identify the hazards associated with the use of the EWP and implement control measures to eliminate or minimise those risks so far as is reasonably practicable.
The main hazards related to the use of EWPs are contact with electric lines, overturning the machine, falling from the work platform, and potential crushing hazards when elevating the platform or moving laterally.
CONTROL MEASURES
Relevant risk control measures when using EWPs include:
- training and instructing workers in the safe operating procedures for the particular brand and type of EWP, as well as safe work procedures to avoid crushing and electrical hazards;
- provision of fall arrest / safety harness equipment;
- training and instructing workers in the safe use of fall arrest equipment and emergency rescue procedures;
- observing the safe working load for the EWP;
- ensure the EWP is set up on stable and level ground;
- ensure floor load bearing capacity is adequate;
- check for clearances of objects, structures, and powerlines by walking through the placement and use of the EWP;
- work within the permitter of the EWP platform; and
- maintain the EWP platform’s centre of gravity.
NB 1: The lanyard of the fall-arrest harness should be as short as possible and should be attached directly to the designated anchor point on the EWP, not to the handrail, unless the handrail is the manufacturer’s specified anchor point.
NB 2: If it is necessary to move a SEWP with the boom raised and a person on the platform, ensure the outriggers are no more than 10mm from the floor and the person on the platform is not protruding from the confines of the platform.
Theatrical Flying and Rigging Operations
Responsibility for safe execution of rigging lies with the producer. The Safety Supervisor and the Producer should ensure that the Safety crew are adequately trained, experienced, and supervised to undertake the duties required of them.
Any person undertaking flying operations should hold the appropriate certificate of competency and be competent to operate the relevant equipment. They should:
- only ever rig loads appropriate to their level of training – if in doubt, ask;
- ensure that all persons are protected from injury by means of appropriate barriers;
- check braking systems of flying systems prior to use;
- test that cabling and winches of flying systems are in line with manufacturer’s recommendations; and
- maintain a lifting register for all cables and ropes.
Safe working practices for flying and rigging include:
- never exceed safe working loads;
- ensure items being flown have been designed and constructed in a manner appropriate for flying;
- ensure flown items are securely fastened to scenery bars;
- when lowering scenery, warn those below (during a performance this will be via appropriate communications systems);
- use steel slings as a secondary for fibre slings if there is a risk of fire;
- use packing between slings and sharp edges; and
- lower loads onto timber to avoid sling crushing.
Considerations in respect of movement of people include:
- no-one should ever ride on hooks, slings, or loads;
- use a safety factor of 10:1 when suspending people;
- use safety lines with ratings in accordance with Australian Standards; and
- plan aerial performance sequences with appropriate rigging for the size of the performer(s) and the task to be completed – include consideration of the need for crash mats, safety netting, appropriate emergency, and contingency procedures – lighting, set or sound changes should be communicated to both riggers and aerial performers.
Flexible Steel Wire Rope Rigging (FSWR) and Synthetic Rope Rigging
Any rigging involving FSWR should only be undertaken by riggers holding relevant certification.
Any rigging involving FSWR, potential shock loads and the possibility of a pendulum effect should be carried out only by trained Stunt Rigger/s.
+ Machinery and power tools
DANGEROUS MACHINERY
Dangerous machinery includes any engine, motor, shaft, belt, gearing, pulley, flywheel, contrivance, or appliance operated by any source of motive power.
PCBUS
PCBUs are responsible for making sure the hazards associated with machinery are controlled in the workplace, so they do not harm workers and operators.
Duty holders should use the Australian Standard (AS) 4024 Safety of Machinery to identify procedures to safeguard machinery and plant. The employer must make sure that any competent person they hire to give advice or services on machine guarding or safe use of machinery is experienced in using AS 4024, or equivalent or higher standards.
HAZARDS
Hazards can be mechanical or non-mechanical.
CONTROL MEASURES – MECHANICAL HAZARDS
Where exposure to machinery and equipment hazards cannot be eliminated or substituted for machinery and equipment of improved design, risk controls must be applied to the hazards to prevent or reduce the risk (chance) of injury or harm. Key controls include:
- physical barriers and guards, such as fences, screens, or fixed panels of various materials;
- various forms of guarding and interlocking (as described in AS4024, parts 1601 and 1602, Safety of Machinery);
- making the hazard inaccessible by reach (where the distance between a person and the hazard forms an effective barrier); and
- provision of PPE.
All dangerous machinery should be adequately guarded in accordance with manufacturer’s recommendations and statutory requirements. Except for maintenance purposes, machine guards should not be removed.
GUARDING
Employers should ensure that all machine guards are effective and appropriate for the machine. All machine guarding should comply with AS 4024 – 1996 Safeguarding of Machinery. Guards should be maintained in a serviceable condition.
All safety control systems should be designed and built to prevent failure or, in the event of failure, de-activate the operation of the machinery and equipment.
CONTROL MEASURES - NON-MECHANICAL HAZARDS
The first step in selecting suitable and effective controls for non-mechanical hazards is to understand the nature of emissions that can be released by machinery and equipment and the way they may cause harm.
Hazardous machinery and equipment emission controls rely largely on isolating of people from the hazardous emission. Hoods, lids, covers or impervious guards (solid barriers that prevent escape of the emission) can serve to contain a number of different types of emissions within machinery and/or equipment.
For potentially harmful substance exposures from machinery and equipment, such as mist, fumes, vapour, or dust, and where it is not possible to control the emission at its source, ventilation and extraction systems are used to remove the hazardous emissions from the work environment.
Guarding may also serve to mute noise emissions through application of sound absorbing materials. Other emissions, such as lasers, ultraviolet light, bright light or welding flash, can also be safely screened to prevent potential harmful exposure.
PERSONAL PROTECTIVE EQUIPMENT
Where it is not possible for emissions to be controlled at their source, or removed or reduced through effective ventilation, extraction or diversion, the use of personal protective equipment (PPE) as a final measure must be used to ensure safety.
As in other areas of risk management, PPE is a lower order control and can only be used where higher order controls are not possible or are not totally effective. All PPE should comply with the relevant Australian Standards.
EXPLOSIVE POWERED TOOLS (EPTS)
Explosive-actuated tools use an explosive cartridge or gas discharge to fire a fastener into hard materials such as concrete, mild steel, and masonry. Explosive Powered Tools are specifically referred to in work health and safety regulations and fall into the category of plant that requires the employer to identify all hazards to health and safety with the use of the plant and associated systems of work.
PCBU
PCBUs are required to ensure that any person using an EPT in the workplace is an appropriately trained and qualified operator who holds the appropriate certificate of competency and uses the tool in a safe manner. PCBUs are also required to provide such information, instruction, training, or supervision to employees as is necessary to enable those persons to perform their work in a way that is safe and without risks to health.
CONTROL MEASURES
- Only use explosive power tools that have been designed according to AS/NZS 1873:1994 – Power-Actuated (PA) Handheld Fastening Tools.
- Only use explosive power tools that display the manufacturer’s name, the serial number, the model number and a misfire warning and instructions for safe operation.
- Tools must be inspected and function-tested before work starts. Proper training and the operator’s manual will describe how to carry out both requirements.
- Operators must be trained on the explosive-actuated tools they are using and must wear all the required personal protective equipment.
- Storage of charges should be in a secure and clearly marked container.
The following checklist offers further sound guidance about risk management and control.
Do not:
- Use an EPT unless it is fitted with an effective muzzle guard, shield, or fixture according to the maker’s recommendations for any type of material being fixed.
- Load the EPT until ready for immediate use.
- Leave an EPT unattended or put away or carry to another place or transport any tool which is charged. Remove the charge and projectile – check to make sure the tool is unloaded before altering, adjusting, removing, or changing muzzle, safety guards or barrel extensions.
- Point the tool, loaded, or unloaded, towards yourself or towards other persons, no matter how far away they are.
- Use the EPT unless warning signs are displayed near the place where the tool is being used.
- Use a EPT without the operator and any assistant wearing approved safety goggles complying with AS 1337 Industrial Eye Protectors.
- Fire the EPT at an angle - make sure the tool is perpendicular to the work surface.
- FIRE an EPT from a ladder – use a fixed platform to enable correct aim and pressure.
- Use an EPT in any places where flammable gas or dust or vapour is or may be present, or in compressed air, or in any place where the explosive charge might be exploded or rendered dangerous by heat.
- Attempt to drive a projectile into concrete and mild structural steel unless a check has been made to ensure it is of sufficient thickness to prevent the projectile passing completely through.
- Use EPT charges in other firearms; this is very dangerous; keep the “explosive” container locked at all times except when cartridges are being placed therein or removed there from.
- Use the high charges first.
- Fire an EPT on a surface that is covered in loose particles.
- Use an EPT on a fastener already in situ to push the fastener in deeper.
- Leave failed charges lying around.
MISFIRES
With misfired cartridges, follow the procedures stated in the operating manual. If the manual is not available:
- continue to hold the tool against the base material for at least 30 seconds;
- remove the cartridge from the tool, keeping the tool pointed safely toward soft material such as wood. Never use any kind of prying device to extract the cartridge from the chamber; and
- place misfired cartridge in a container of water.
+ Hot work procedures
‘Hot work’ is a term used to describe the potential to generate heat, flames, or sparks. Examples include:
- welding;
- burning;
- flame cutting;
- brazing/soldering;
- plasma cutting;
- grinding; and
- metal spraying.
Hot works are the second largest cause of fires within buildings.
HAZARDS
The hazards associated with hot work include:
- explosion when cutting up, repairing, or working on or in the vicinity of drums, tanks, pipes or vessels which contain or have contained flammable liquids, gases or materials;
- fire/explosion caused by a gas leak, or flammable liquids or materials backfire or flashback;
- burns from contact with the flame, sparks, molten metal, or hot metal;
- crush or impact injuries resulting from an explosion;
- exposure to toxic fumes; and
- depletion of oxygen levels in the atmosphere causing suffocation.
PCBU
Prior to carrying out any hot work on site it is essential to implement a hot work permit system, which includes a detailed review, to identify all potential hazards associated with the proposed hot work activity and to eliminate the hazards or, where this is not reasonably practicable, control the resulting risks.
The hot work permit system should incorporate a check list to address all hazards and controls and should be reviewed and signed off by the persons in control of the site and involved in the hot work activity. Hot work procedures should be performed in accordance with Australian Standard (AS) 1674.1 – 1997 Safety in Welding and Allied Processes Part 1 Fire Precautions.
The script breakdown safety report should highlight scenes requiring hot work processes. The head of the Art Department / SFX Coordinator should then arrange for a risk assessment / SMWS to be undertaken and the results shared with all relevant personnel.
CONTROL MEASURES
Typical control measures – whether factored into the permit system or not - include:
- ensure the area in which work is to occur is not a confined space;
- identify and control any fire hazard inside and outside the work area, including flammable or combustible liquids, gases, vapours, dusts, fibres, wood, paper, textiles, packaging, plastics, tyres, dry grass, or other substances within 15 metres of the hot work;
- so far as reasonably practicable, remove any flammable or combustible material found, or otherwise provide non-flammable covers or screens to control sparks and flash in the confined space and its surrounds;
- locate and protect, and if reasonably practicable isolate, all services;
- ensure the area is adequately ventilated;
- ensure gas cylinders are not damaged and fitted with flash back arresters;
- ensure adequate firefighting equipment is ready for use;
- limit personnel and vehicle traffic in the area;
- utilise a fire watch person to monitor the hot work environment;
- isolate and secure the area to prevent unauthorised access and erect appropriate signage;
- establish emergency and evacuation procedures and train all personnel; and
- ensure relevant workers are wearing appropriate non-flammable personal protective equipment.
Inspections of the hot work area should be undertaken for four hours following completion of the work to ensure there is no re-ignition.
+ Electrical work
AUSTRALIAN STANDARD
The Standard, AS/NZS 4249, Electrical safety practices for Film, video and television specifies the requirements for safe working practices in the use of electrical equipment on film, video and television sites and the in-service testing of equipment. AS/NZS 4249 outlines the minimum safety requirements for the use of temporary electrical installations which supply electricity to appliances and equipment on film, video and television sites including in-service testing of portable and transportable equipment.
The Standard applies to any temporary installations, portable distribution systems, appliances and equipment connected to temporary electrical supply in connection with dry hire studios, any buildings and their environs used as temporary studios and interior/exterior locations and all outside broadcasting.
The Standard outlines a range of specific safety measures in connection with:
- general electrical safety procedures;
- the use of residual current devices (RCDs);
- the protection of cables, cords and cord extension sets;
- portable distribution boards;
- generating sets;
- earthing and bonding; and
- equipment testing and recording.
The most common electrical risks and causes of injury are:
- electric shock causing injury or death. The electric shock may be received by direct or indirect contact, tracking through or across a medium, or by arcing. For example, electric shock may result from indirect contact where a conductive part that is not normally energised (such as a metal toaster body or a fence) becomes energised due to a fault;
- fire (such as fire resulting from an electrical fault), arcing or explosion causing burns. These injuries are often suffered because arcing or explosion or both occur when high fault currents are present;
- electric shock from ‘step-and-touch’ potentials; and
- toxic gases generated by burning and arcing associated with electrical equipment.
Even the briefest contact with electricity at 50 volts for alternating current (V a.c.) or 120 volts for direct current (V d.c.) can have serious consequences for a person’s health and safety. High voltage shocks (involving more than 1000 V a.c. or 1500 V d.c.) can cause contact burns and internal injury.
Electric shocks may also lead to other injuries, including falls from ladders, scaffolds, or other elevated work platforms.
PCBU
A PCBU must eliminate electrical risks or, if that is not reasonably practicable, minimise the risks so far as is reasonably practicable.
Inspections and testing must be carried out by a competent person, which depending on your jurisdiction might be a licensed or registered electrician or a licensed electrical inspector. The nature and frequency of inspection and testing depends on factors such as the nature of the electrical equipment, how it is used, and its operating environment.
Workers have a duty to take reasonable care for their own health and safety and to not adversely affect the health and safety of other persons. Workers must comply with reasonable instructions, as far as they are reasonably able, and cooperate with reasonable health and safety policies or procedures that have been notified to workers. This means that if electrical equipment or personal protective equipment (PPE) is provided by the PCBU, the worker must use it, so far as they are reasonably able, in accordance with the information, instruction and training provided about its use.
Production companies and producers must:
- engage competent, qualified persons to oversee and undertake all electrical work associated with the production;
- consider the potential risks associated with electrical work when planning and allocating tasks;
- ensure the potential risks associated are appropriately managed, either eliminating or minimising them; and
- consider whether a specialist company may be required to produce a suitable electrical design.
RESIDUAL CURRENT DEVICES (RCDS)
One of the minimum requirements set out in AS/NZS 4249 is the installation of an RCD – commonly referred to as a safety switch. This is an electrical safety device designed to immediately switch off the supply of electricity when electricity ‘leaking’ to earth is detected at harmful levels.
RCDs offer high levels of personal protection from electric shock. While RCDs significantly reduce the risk of electric shock, they do not provide protection in all circumstances. For example, an RCD will not trigger the switching off of electricity supply if a person contacts both active and neutral conductors while handling faulty plugs or electrical equipment and electricity flows through the person’s body, unless there is also a current flow to earth.
RCDs should comply with AS 3190. RCDs with a rated residual current not exceeding 30 mA should be installed to protect:
- all socket outlets;
- all final sub-circuits; and
- all individual circuits.
Ensure that every RCD is functionally trip-tested by a competent person using the RCD test button daily before use, or prior to the commencement of each operational period; and subjected to an operational performance test with an RCD tester, in accordance with the requirements for portable RCDs in AS 3760, conducted by a competent person every three months. It is important to keep records of tests, including the dates and results of tests.
If RCDs, circuit breakers or other protective devices including fuses are triggered into operation, ensure circuits are not re-energised until the reason for the operation has been determined by a competent person.
TESTING EQUIPMENT
Although brand new electrical equipment that has never been put into use (i.e., other than second-hand equipment) does not have to be tested before first use, it should still be visually inspected to ensure that no damage occurred during transport, delivery, installation, or commissioning.
If the electrical equipment is required to be tested regularly for safety, take steps to ensure that it does not miss required tests. The date the electrical equipment was placed into service should be recorded. It should also be fitted with a tag stating:
- that the equipment is ‘new to service’ and its date of entry; and
- the date when the first electrical safety test is due.
HIRE EQUIPMENT AND APPLIANCES
Ensure that all electrical equipment or appliances hired for a site are inspected, tested, tagged, and recorded at the supplier’s premises at the start of each hire and then tested every three months. It is the responsibility of the person who has hired the electrical equipment or appliances to meet the conditions of testing, tagging, and recording as required during the period of hire.
Inspection and testing of electrical equipment must be carried out by a competent person. A competent person includes a person who is licensed or registered to perform electrical work under a law relating to electrical safety or occupational licensing.
Consider eliminating the use of metallic, wire reinforced or otherwise conductive ladders when installing or using electrical equipment. Metallic or wire reinforced ladders and scaffolds are conductive and may create an electric shock. These types of ladders should be avoided for any kind of electrical work and should not be used near equipment where an electrical hazard may result from their use.
Also consider the electrical risks posed when using ladders, scaffolds, and similar equipment, including that workers are more likely to touch open wiring such as overhead lines, and portable scaffolds may damage insulation when moved if the scaffold strikes conductors or leads.
CABLES, CORDS AND LEADS
Cables must be in positions where they are not subject to damage by mechanical devices or liquids. A production must ensure that:
- cables are secured and clearly identified;
- leads are off the ground or protected where practicable, including away from potential mechanical damage or intrusion by liquids;
- electrical equipment/devices are protected from the weather, or constructed to a suitable IP rating;
- cables and distribution are of sufficient size and capacity to do the required job;
- cables are not twisted, crushed, or kinked;
- leads should never be run across roads or any area subject to vehicular access;
- flexible cords and cables should not be used while in a coiled or reeled configuration;
- so far as is reasonably practicable, avoid running leads across the floor or ground, through doorways and over sharp edges; use lead stands, insulated cable hangers and/or cable protection ramps; and
- cable routing is carefully considered and does not create a tripping hazard.
If it is not possible to keep leads off the ground, appropriate controls should be implemented with consideration being given to the use of covers.
AS/NZS 4249 states that overhead cables may be supported so long as the span does not exceed 45 metres, with spans exceeding 13 metres supported by catenary wire.
Where cables are supported overhead, there must be a minimum clearance of 4.5 metres for vehicular traffic occurs and 2.5 metres in all other instances.
Where cables need to be moved manually in conjunction with dollies, cameras, booms, etc.:
- cables should be kept as short as possible;
- adequate numbers of cable runners shall be utilised;
- the sequence/s should be rehearsed;
- the path of the cable runner/s should be kept clear;
- all those in the vicinity should be aware of the cable running; and
- when laying, and retrieving cables, they should be looped loosely rather than coiled tightly to minimise overheating of cable insulation and to avoid entanglement.
All Telsa Coils and other non-standard electrical equipment designed to be used in conjunction with creating special effects should be appropriately guarded and inspected, tagged, and tested in accordance with AS/NZS 3760:1996 – In Service Inspection and Testing of Electrical Equipment and/or other relevant regulations covering the use and operation of such equipment.
LIGHTING FIXTURES AND PORTABLE ELECTRICAL EQUIPMENT
Equipment should be electrically isolated from the power source before proceeding to work on it, e.g., changing light bulbs/lamps. In addition:
- all lighting fixtures or equipment should be adequately supported or mounted to prevent tipping or falling;
- suspended equipment should have a separate safety chain or cable to prevent falling;
- the chain or cable should have welded links or be made of wire rope;
- static load rating of safety chain or cable should be 10:1;
- any open-faced lighting unit should have protection where practicable (wire mesh, safety glass) against the shrapnel effect caused by an exploding bulb/lamp, particularly when near people;
- every lamp holder of the Edison screw type should be connected to the supply so that where a neutral conductor is required it should be connected to the outer contact;
- all electrical equipment not appropriately IP rated should be covered in adverse conditions to prevent water from entering the equipment; and
- underwater lights and equipment rated above 32 V a.c. and fixtures should have a degree of protection IPX8 and be protected by an RCD having a rated residual current not exceeding 30 mA.
Steps to protect production workers from ultraviolet lights from HMI lamps:
- all personnel on site should be advised that various ‘arc’-type lamps, including HMIs, emit much larger amounts of ultraviolet (UV) radiation than tungsten lamps;
- care should be taken to protect against skin and eye damage when they are set up close to people;
- various filters are available to reduce UV light;
- all HMIs should be used with UV filters. Fixtures should not be used if the filters are cracked or broken. Micro switches should not be bypassed;
- a UV filter/gel should be used in conjunction with a clear glass filter when using open-faced HMI lamps to minimise the incidence of headaches and eye damage and to provide protection against exploding bulbs; and
- the use of any combustible material near lamps should be avoided to prevent fire or the emission of dangerous fumes.
Portable outlet devices shall comply with AS 3100 and shall be constructed of durable, impact-resistant materials.
Portable distribution boards shall be of robust, non-corrosive design and the socket outlets and associated control gear shall be protected against mechanical damage. When used outdoors, they shall be protected against the weather with minimum IP23 degree of protection.
GENERATORS
All connections to a generating set shall be made by a competent person. All generators must have an earthing system suitable to operate an RCD. The main breaker shall be fitted with an RCD. Generators shall be tested every 6 months.
On all exterior night shoots, where a stunt or other hazardous situation may develop, due to a blackout (however caused), an alternative source of supply shall be available to operate sufficient lighting for safety.
EMERGENCY PLANNING
Fire extinguishers suitable for electrical fires shall be available on all production sites.
Fire extinguishers suitable for electrical and oil fires shall be carried on generating sets used at production sites.
A well-prepared emergency response will assist in managing the severity of the injury where an incident has occurred, while also taking into account the health and safety of those required to respond to the incident. For example, in an exposed energised high voltage situation, the plan may include isolating the electricity supply and proving it is de-energised before carrying out a rescue.
Some of the features of an emergency plan will be:
Don't touch someone receiving an electric shock
A charge that has passed through your co-worker could easily move into you if you make contact with them. Given that electricity has the capacity to kill or seriously injure, limiting the number of people exposed to the shock should be your number one priority. Be especially wary of incidents that occur in the vicinity of water and other liquids.
Call emergency services
Victims of serious electric shocks will need treatment from medical professionals. Call emergency services and give as much detail as possible about what has happened.
Turn off the power
If it's safe to do so without putting yourself in danger, turn off the power to make the site safer and prevent further harm/damage. If the power cannot be turned off safely, try to separate the victim from the electricity source using a dry, non-conductive item such as a wooden broomstick, or the rescue crook from a low voltage rescue kit if one is readily available.
Administer first aid
Only once the victim is away from the current can you approach them and begin first aid.
- If the individual is responsive – Attend to their injuries, for example place burns under cold water for 20 minutes, and then cover with dressings. If you don't have a first-aid kit with you, kitchen glad wrap is suitable, as long as it's not applied too tightly. Never put oils or ointments on burns.
- If the individual isn't breathing – For unconscious victims who aren't breathing, perform cardiopulmonary resuscitation (CPR) until medical teams arrive to take over from you.
See also: G5 for template Emergency Plan.
+ Manual handling and lifting
This section covers ordinary and hazardous manual handling processes, noting that occasional manual handling duties may also align with those described as ‘hazardous’.
Manual handling is any activity that involves lifting, pushing, pulling, carrying, moving, holding, or restraining. It also includes sustained and awkward postures or repetitive movements.
A hazardous manual task is a task requiring a person to lift, lower, push, pull, carry, or otherwise move, hold or restrain any person, animal or thing involving one or more of the following:
- repetitive or sustained force;
- high or sudden force;
- repetitive movement;
- sustained or awkward posture; or
- exposure to vibration.
These hazards directly stress the body and can lead to an injury, such as musculoskeletal disorder (MSD). ‘MSD’ refers to an injury to, or a disease of, the musculoskeletal system, whether occurring suddenly or over time. An MSD may include:
- sprains and strains of muscles, ligaments, and tendons;
- back injuries, including damage to the muscles, tendons, ligaments, spinal discs, nerves, joints, and bones;
- joint and bone injuries or degeneration, including injuries to the shoulder, elbow, wrist, hip, knee, ankle, hands, and feet;
- nerve injuries or compression, for example carpal tunnel syndrome;
- muscular and vascular disorders as a result of hand–arm vibration;
- soft tissue injuries including hernias; or
- chronic pain.
An MSD can occur through gradual wear and tear to joints, ligaments, muscles, and inter-vertebral discs caused by repeated or continuous use of the same body parts, or through sudden damage caused by strenuous activity, or unexpected movements such as when loads being handled move or change position suddenly.
PCBU
A PCBU must eliminate risks arising from hazardous manual tasks, or if that is not reasonably practicable, minimise the risks so far as is reasonably practicable.
PCBUs have a duty to consult workers about work health and safety and may also have duties to consult, cooperate and coordinate with other duty holders.
Workers and other persons at the workplace also have duties under the WHS Act, such as the duty to take reasonable care for their own health and safety at the workplace. A person can have many more than one duty and more than one person can have the same duty at the same time. Early consultation and identification of risks can allow for more options to eliminate or minimise risks and reduce the associated costs.
A PCBU must manage risks to health and safety relating to a musculoskeletal disorder associated with a hazardous manual task. In order to manage risk under the WHS Regulations, a duty holder must identify reasonably foreseeable hazards that could give rise to the risk, eliminate the risk or minimise the risk so far as is reasonably practicable by implementing control measures in accordance with the hierarchy of control measures.
CONTROL MEASURES
PCBUs and workers must always take into account of:
- individual capability;
- the nature of the load;
- environmental conditions; and
- training (where applicable) and work organisation.
When lifting manually:
- reduce the amount of twisting, stooping, and reaching;
- reduce carrying distances where possible;
- avoid lifting from floor level or above shoulder height, especially heavy loads;
- adjust storage areas to minimise the need to carry out such movements;
- consider how you can minimise carrying distances;
- assess the weight to be carried and whether the worker can move the load safely or needs any help – maybe the load can be broken down to smaller, lighter components;
- remove obstructions from the route;
- for a long lift, plan to rest the load midway on a table or bench to change grip;
- keep the load close to the waist. The load should be kept close to the body for as long as possible while lifting;
- keep the heaviest side of the load next to the body; and
- adopt a stable position and make sure your feet are apart, with one leg slightly forward to maintain balance.
Before an object is lifted, assess the start and finish heights, and ensure clear pathways. For objects over 16kg use mechanical aids or, as a last resort use two or more people. For large (awkward) objects (even light ones) use mechanical aids or a two-person lift.
If a production involves lifting of equipment, especially on a regular basis, the steps in the following table should be considered.
+ Confined spaces
A confined space means an enclosed or partially enclosed space that:
- is not designed or intended to be occupied by a person;
- is at normal atmospheric pressure—or is designed or intended to be at normal atmospheric pressure—while a person is in the space;
- is a risk to health and safety from:
- an atmosphere that doesn’t have a safe oxygen level; and
- contaminants like airborne gases, vapours and dusts that may cause injury from fire or explosion;
- has harmful concentrations of any airborne contaminants; and
- is at risk of engulfment through fire and/or explosion.8
Confined spaces are commonly found in vats, tanks, pits, pipes, ducts, flues, chimneys, silos, containers, pressure vessels, underground sewers, wet or dry wells, shafts, trenches, tunnels or other similar enclosed or partially enclosed structures.9
Confined spaces may pose a danger because they are not designed to be areas where people work. Hazards are not always obvious, may change and the risks include loss of consciousness, impairment, injury, or death.
The senses cannot be relied upon to determine if the air in a confined space is safe. Many toxic gases and vapours are odourless and colourless and therefore cannot be detected by sight or smell.
PCBU
A PCBU must eliminate or minimise risks associated with work practices and the atmosphere in a confined space, so far as is reasonably practicable. A risk assessment must be undertaken to identify hazards and then implement control measures.
RISK ASSESSMENT
The risk assessment will consider:
- whether the work can be carried out without the need to enter the space;
- the nature of the space;
- the hazards associated with the space, including the substances therein;
- the risk of engulfment of a person;
- the number of persons required outside the space to maintain equipment and communications; and
- arrangements for emergency response, for example first aid and resuscitation.
A safe atmosphere in a confined space is one that:
- has a safe oxygen level;
- is free of airborne contaminants or any airborne contaminants are in concentrations below their allowable exposure standard (if any); and
- any flammable gas, vapour or mist in the atmosphere is at concentrations below 5 per cent of its lower explosive level (LEL).
As a PCBU, you must also ensure that openings for entry and exit are of a sufficient size to allow emergency access, openings are not obstructed, and any plant, equipment, and personal protective equipment (PPE) provided for first aid or emergency rescue are maintained in good working order.
Everyone needs a permit to enter the space. Permits ensure a safe system of work is in place and ensures communication between site management, supervisors and those carrying out the work.
CONTROL MEASURES
Some of the control measures to be employed for confined space works include:
- cleaning, purging and ventilation of space;
- the adequate instruction of persons in any required procedure;
- advice concerning the use and limitations of any PPE and other equipment to be used;
- the provision of emergency equipment for all persons likely to enter the confined space;
- prohibiting hot work in adjacent areas;
- prohibiting smoking and naked flames within the confined space and adjacent areas;
- avoiding contamination of breathing air from operations or sources outside the confined space, for example from the exhaust of an internal combustion engine;
- prohibiting movement of equipment in adjacent areas, for example forklifts;
- prohibiting spark-generating equipment, clothing, and footwear; and
- ensuring communications between those in the confined space and persons keeping watch outside.
Finally, PCBUs must also establish first aid and rescue procedures to be followed in an emergency and ensure that workers practise those procedures to ensure that they are efficient and effective. First aid and rescue procedures must be initiated from outside the confined space as soon as practicable in an emergency.
+ Working below ground / excavation
PCBU
Producer, Construction Supervisor, Production Designer, Safety Supervisor (or equivalent)
In order to manage risks under the WHS Regulations, a PCBU must identify reasonably foreseeable hazards that give rise to risks and eliminate the risk so far as is reasonably practicable. If it is not reasonably practicable to eliminate the risk – minimise the risk so far as is reasonably practicable by implementing control
Critically, a PCBU must take all reasonable steps to obtain current underground essential services information relating to the part of a workplace where the excavation work is being carried out and areas adjacent to it before directing or allowing the excavation to commence. This information must be provided to any person engaged to carry out excavation work.
Workers also have a duty to take reasonable care for their own health and safety and that they do not adversely affect the health and safety of other persons. Workers must comply with any reasonable instruction and cooperate with any reasonable policy or procedure relating to health and safety at the workplace.
CONTROL MEASURES
Before any work below ground begins, appropriate plans should be approved by the producer or their delegate, including ensuring that:
- problems with electrical, water, gas, or telephone pipes/lines in the area will not arise or otherwise be subject to appropriate management protocols;
- air quality in any trench is satisfactory;
- emergency and rescue procedures and equipment are in place, including provision of alternative access and egress points;
- appropriate access and exits will be established;
- all trenches, pits and traps are barricaded and/or appropriately signed;
- spoil heaps are kept well away from evacuations;
- consideration is given to what could fall into or otherwise affect what is being done below ground;
- shoring (where necessary) is adequate and in line with requirements, e.g., for nearby traffic;
- installing landing platforms or scaffold towers inside deep excavations; and
- installing effective barriers or barricades.
With respect to machinery/plant to be used, Control measures include:
- plant is used and operated by a competent person;
- that appropriate guards and operator protective devices are fitted;
- that the safe working load is displayed, and any load measurement devices are working; and
- plant is maintained in accordance with the manufacturer/supplier’s instructions and/or relevant Australian Standards.
The following table outlines possible hazards and associated control measures.
Where there is a risk of falls, WHS Regulations require the following specific control measures to be implemented where it is reasonably practicable to do so:
- if a fall risk cannot be eliminated, minimise the risk of fall by providing and maintaining a safe system of work including using fall prevention devices (e.g., temporary work platforms and guard rails);
- work positioning systems (e.g., industrial rope access systems); or
- fall arrest systems such as catch platforms.
Risk of atmospheric contamination through a build-up of gases and fumes must be controlled in excavation work. Plant that uses a combustion engine (e.g., air compressors, electrical generators) should never be used in a confined excavation such as a trench if workers are in the trench. The build-up of exhaust gases in the excavation, particularly carbon monoxide, can cause death.
Ventilation systems help to maintain adequate oxygen levels and dilute flammable gases, fumes, and certain dusts, such as coal and sulphide which can ignite if in its explosive limits. The use of mechanical ventilation also reduces dust, fumes, hazardous contaminants and can control air temperature and humidity.
Any remaining risk must be minimised with suitable Personal Protective Equipment (PPE), such as hard hats, hearing protection and high visibility vests.
+ Hazardous substances
A hazardous substance is any product or chemical that has explosive, flammable, oxidising, toxic, corrosive or ecotoxic properties. Hazardous chemicals may present an immediate or long-term risk to human health through their toxicological properties (health hazards), or a risk to safety of persons and property as a result of their physical hazards. In some cases, chemicals may present both health and physical hazards.
PCBU
Producers, Head(s) of Department, Safety Supervisor, Stunt Coordinator
Where the hazards and associated risks are well-known and have well established and accepted control measures, it may not be necessary to undertake a risk assessment, for example, where there are a small number of chemicals in a workplace and the hazards and risks are well understood. In other cases, it may be necessary to seek external professional assistance to assist or undertake risk assessments.
A PCBU has the primary duty to ensure, so far as is reasonably practicable, that the health and safety of workers and other persons are not put at risk from work carried out as part of the conduct of the business or undertaking. This includes ensuring the safe use, handling, and storage of substances.
PCBUs and their properly delegated representatives are responsible for developing and implementing safe systems of work in consultation with employees and ensuring that persons using chemicals are competent in handling dangerous substances and strictly adhere to prescribed working practices.
Workers and other persons at the workplace also have duties under work health and safety laws, such as the duty to take reasonable care for their own health and safety at the workplace. All workers must:
- follow all health and safety information, training, and instruction they have received;
- must be aware of what personal protective equipment they are expected to provide themselves and what will be provided by the production; and
- follow instructions provided by the person in charge of any activity that involves the use of, or is conducted near, hazardous substances.
CONTROL MEASURES
Hazardous substances must only be used by people with knowledge about the substance, its health effects and emergency procedures. Anyone handling or working with hazardous substances needs to:
- be trained or supervised in safe handling procedures;
- be provided with information and MSDS about the product;
- understand the health hazards associated with the hazardous substances;
- ensure their safety, and the safety of others, when using the hazardous substances; and
- know the actions to be taken in an emergency involving the hazardous substances.
SAFETY DATA SHEET / MATERIALS SAFETY DATA SHEET
The identity of chemicals in the workplace can usually be determined by looking at the label and the SDS (Safety Data Sheet) – also known as Material Safety Data Sheet (MSDS). Suppliers of hazardous substances are responsible for providing a copy of the MSDS which has been prepared by a manufacturer or importer.
An SDS provides critical information about hazardous chemicals, including:
- the chemical's identity and ingredients;
- health and physical hazards;
- safe handling and storage procedures, including storing in areas free of ignition sources;
- emergency procedures; and
- disposal considerations.
SDS/MSDSs also provide information about how to minimise risks associated with the storage, handling, use and disposal of hazardous substances.
All substances used in the workplace should be appropriately and clearly labelled. Labels should be:
- on an outside face of the container;
- in readable, distinctive, and durable print, including for signifiers, such as ‘FLAMMABLE’; and
- robust enough to withstand fair wear and tear while being handled by users.
The PCBU must ensure the current SDS/MSDS is readily accessible to workers involved in using, handling, or storing the hazardous chemical at the workplace and emergency service workers, or anyone else who is likely to be exposed to the hazardous chemical.
In most circumstances, PPE should not be relied as a control measure. It should be used only as a last resort when all other reasonably practicable control measures have been used and the risk has not been eliminated, or as interim protection until higher level controls are implemented.
As producers and production managers have oversight across the production, they should:
- communicate to all personnel the presence and/or use of hazardous substances;
- provide appropriate information on safety matters should be included;
- ensure workers are provided appropriate personal protective equipment;
- ensure workers are wear appropriate personal protective equipment;
- ensure that emergency and first aid procedures are in place;
- ensure sufficient firefighting equipment is provided and that it is immediately available on set if required; and
- ensure there is a clear access way for emergency and firefighting equipment and vehicles on set.
Heads of departments should:
- ensure workers using hazardous substances carry the necessary skills, certifications and / or experience for the discrete work being performed in their department(s);
- all workers on site know of the existence and use of hazardous substances;
- ensure hazard identification and risk assessments are undertaken for all activities using hazardous substances, and controls implemented;
- ensure that emergency and first aid procedures are followed; and
- ensure personal protective equipment specific for hazardous substance work is provided to, and used by, workers when required.
Other general control measures include:
- only use chemicals if necessary;
- quantities of chemicals should be kept to an absolute minimum;
- all users should be trained in safe systems of work;
- chemicals should be stored in properly labelled, appropriate containers, handled, and disposed of properly
- keep work areas well-ventilated;
- guard or enclose heating elements and other electrical equipment to prevent ignition or decomposition of any nitrocellulose products; and
- keeping the temperature of any surfaces and equipment (including enclosures) to a suitably safe temperature for the material being used.
EMERGENCIES
Regardless of controls put in place to prevent incidents occurring in your workplace, they can still occur. As a PCBU that uses, handles, generates, or stores hazardous chemicals must ensure that equipment is always available at the workplace for use in an emergency. Equipment must be located so it is readily accessible for all workers if an emergency arises.
In the event of spills, a PCBU must ensure, so far as is reasonably practicable, that where there is a risk of a spill or leak of a hazardous chemical in a solid or liquid form, provision is made for a spill containment system.
A spill or other misadventure can result in production staff being exposed to chemicals and requiring immediate medical treatment and/or a fire can start. It is therefore necessary to be prepared for any foreseeable incident.
At a minimum, emergency procedures should include instructions on:
- an effective response to an emergency, including access to first aid materials;
- evacuation procedures;
- notification procedures to advise emergency services organisations at the earliest opportunity;
- medical treatment and assistance; and
- communication procedures between the person coordinating the emergency response and all persons at the workplace.
Nitrocellulose film and other nitrocellulose products—handling and storage
Nitrocellulose film and products containing nitrocellulose can represent a significant explosion hazard if the risks are not properly controlled. Risks can be minimised by:
- reducing the amount of material stored or handled in the work area at any one time;
- ensuring the storage and handling area is constructed from non-combustible materials;
- ensuring there is sufficient means of escape in the event of an emergency. For example, use of outward opening doors, and removing all non-essential furniture and equipment from the work area to allow unimpeded access to the emergency exit; and
- eliminating ignition sources.
+ Working in high temperatures
Working in heat can be hazardous and can cause harm to workers. The human body needs to maintain a body temperature of approximately 37 degrees Celsius.
PCBU
The PCBU must ensure, so far as is reasonably practicable, production workers are not exposed to health and safety risks arising from the business or undertaking. This duty requires the person to manage health and safety risks by eliminating them so far as is reasonably practicable, and if this is not reasonably practicable, by minimising those risks so far as is reasonably practicable.
RISK ASSESSMENT
It is vital to consider the working environment/conditions:
- Is the work physically demanding? Physical effort increases the risk of heat-related illness, even in moderate conditions.
- How long will the worker be exposed to heat? When and where can they take breaks? Extended exposure to heat makes it harder for the body to stay cool.
- Could anything prevent a worker from pacing their work?
- Is the work complex or difficult? Concentration may be affected by heat.
- Is the worker physically fit and are they acclimatised to the current environment?
- Are workers required to wear clothing such as personal protective equipment (PPE)?
- Clothing that impairs the evaporation of sweat increases the risk of heat-related illness.
CONTROL MEASURES
The PCBU must do everything that is reasonably practicable to eliminate the risks associated with working in heat. This may include:
- rescheduling tasks to cooler parts of the day or year; and
- waiting for hot conditions to pass.
If risks cannot be eliminated, the PCBU must minimise it as much as reasonably practicable. Control measures include:
- reorganise outdoor work so that workers carry out alternative tasks, rotate work, or work in shade, particularly 11 am–3 pm when heat and ultraviolet radiation is most intense;
- where possible, use plant or other equipment to reduce manual labour;
- only use work areas that are well ventilated;
- provide fans and shaded or air conditioned break areas;
- provide regular breaks;
- provide accessible, cool drinking water, or when necessary, electrolyte solutions. Encourage frequent water breaks;
- where possible, don’t allow workers to work alone. If they must, then establish procedures for monitoring them and ensuring they can easily seek help;
- provide information, training, and instruction to workers on how to follow safe work procedures, report problems and recognise the symptoms of heat-related illness; and
- provide suitable PPE like a wide brim hat, and sunscreen. Modify the uniform or PPE so that the fabric is lighter and more breathable.
Heat-related injury
When working in heat, dehydration is a major risk. Dark or reduced urine output can indicate dehydration. You can manage the risk of dehydration by providing accessible cool drinking water and encouraging workers to stay hydrated. Water is the best way to keep hydrated. Remember that thirst is satisfied before fluid loss is replaced.
First Aid and Emergencies
Heat-related illness is a progressive condition and if left untreated it can be fatal. If you think someone has severe heat exhaustion, or heat stroke, you should call an ambulance immediately and perform first aid until ambulance arrives.
You have a duty to provide first aid equipment and facilities, and access to trained first aid officers, for sick or injured workers.
Dehydration – Seek medical advice if symptoms don’t improve or are severe
First aid:
- Drink water. Avoid caffeinated, carbonated and alcoholic drinks, and salt tablets.
- Loosen tight clothing and remove unnecessary clothing, including PPE.
- In cases of extreme heat or dehydration, replace electrolytes.
- Drink water. Avoid caffeinated, carbonated and alcoholic drinks, and salt tablets.
Heat rash – Seek medical advice if symptoms don’t improve
First aid:
- Move to a cooler, less humid environment.
- Keep the affected area dry and remove unnecessary clothing, including PPE.
- Apply a cold compress.
Fainting – Seek medical advice
First aid:
- Lie the worker flat immediately with their legs slightly raised.
- Do not raise the head.
- Treat as for heat exhaustion.
Heat exhaustion – Call an ambulance immediately
First aid:
- Move the worker to a cool place with circulating air.
- Lie the worker flat.
- Remove unnecessary clothing, including PPE.
- Loosen tight clothing.
- If the worker is fully conscious sit them up to facilitate drinking and provide cool – not cold – fluid to drink.
- Provide an electrolyte solution or water.
- Cool the worker with cold compresses or apply cold water to skin.
- Observe the worker and obtain medical advice if symptoms don’t improve.
Heat stroke – Call an ambulance immediately
First aid:
- Call 000 and evacuate by ambulance immediately.
- Ensure that the ambulance is updated if the worker experiences seizures or becomes unconscious.
- If cardiac arrest occurs, follow DRSABCD action plan.
- Move the worker to a cool place with circulating air.
- Remove unnecessary clothing, including PPE.
- Loosen tight clothing.
- Cool the worker by splashing room temperature water on their skin or sponging their skin with a damp cloth.
- Make a wind tunnel by suspending sheets around, not on, the worker’s body. Use a fan to direct gentle airflow over the worker’s body.
- Apply cold packs or wrapped ice to the worker’s neck, groin and armpits.
- If the worker is fully conscious sit them up to facilitate drinking and provide cool – not cold – fluid to drink.
- Provide an electrolyte solution with sugar. Do not attempt to give oral fluid if the worker is not fully conscious.
NB: Shivering is an automatic muscular reaction which warms the body. It will make the body temperature rise even further. If the worker starts shivering, stop cooling immediately and cover them until they stop. Once they have stopped recommence first aid treatment.
+ Fatigue
The screen industry is notorious for long hours and tough deadlines. This is generally due to the longstanding practice of making the most economical use of equipment and personnel during a concentrated production period.
Although long and often unsociable hours are often demanded, this does not displace the obligation on persons in control of a production to guard against fatigue and its (often dangerous) consequences.
These guidelines are to be read in conjunction with industrial agreements and contracts, which regulate hours of work, breaks during and between shifts and related matters. (These agreements are discussed in Part D of these guidelines, Employment Agreements.)
PCBU
The PCBU has the primary duty to ensure, so far as is reasonably practicable, workers and other persons are not exposed to health and safety risks arising from the business or undertaking. This includes ensuring, so far as is reasonably practicable:
- provision and maintenance of a work environment without risks to health and safety;
- provision and maintenance of safe systems of work; and
- monitoring the health of workers and the conditions at the workplace for the purpose of preventing illness or injury of workers.
Importantly, the duty on the PCBU is not removed by a worker’s preference for certain shift patterns, their willingness to work extra hours or to come to work when fatigued.
FATIGUE CAUSES
Work causes of fatigue might include:
- prolonged or intense mental or physical activity;
- sleep loss and/or disruption of your internal body clock;
- travel;
- exceptionally hot or cold working environments;
- work scheduling;
- excessively long shifts;
- not enough time to recover between shifts;
- strenuous jobs; and
- long commuting times.
Workers in screen production are often at a high risk of fatigue because their work typically involves some or all of these factors.
Fatigue in the workplace doesn’t only impact on workers’ mental and physical health, it can also impact on the health and safety of those around them.
Fatigue can result in a lack of alertness, slower reactions to signals or situations, and affect a worker’s ability to make good decisions.
IDENTIFYING FATIGUE RISKS
Ways to identify workplace fatigue risks includes checking the production schedule against standard working hours, rostering arrangements, and consulting workers—managers, supervisors and health and safety representatives—about the impact of workloads and work schedules.
Department heads and supervisors should be trained to:
- recognise fatigue;
- understand how fatigue can be managed and how to implement control measures, including how to design suitable rosters and work schedules in consultation with workers; and
- take appropriate action when a worker is displaying fatigue related impairment.
CONTROL MEASURES
The best way to control the health and safety risks arising from fatigue is to eliminate the factors causing fatigue at the source. If elimination is not reasonably practicable, the risks must be minimised.
Control measures for fatigue risks which can be built into a work schedule may include:
- structuring shifts and designing work plans so work demands are highest towards the middle of the shift and decrease towards the end;
- avoiding morning shifts starting before 6am where possible;
- avoiding split shifts or if there is no alternative to split shifts consider their timing, for instance whether they are likely to disrupt sleep;
- setting shift rosters ahead of time and avoiding last-minute changes, to allow workers to plan leisure time;
- allocating shift and night workers consecutive days off to allow for at least two full nights’ sleep including some weekends;
- overlapping consecutive shifts to allow enough time for communication at shift handovers;
- avoiding overtime allocation after afternoon or night shifts;
- keeping sequential night shifts to a minimum;
- providing information to shift workers containing tips for them to prevent and manage the risk of fatigue; and
- developing contingency plans for potential situations where workers may have to unexpectedly work longer hours, more shifts, or a long sequence of shifts.
In addition:
- avoid working during periods of extreme temperature or minimise exposure time through job rotation;
- provide cool/ventilated areas where workers can take a rest break and rehydrate in hot work environments;
- provide adequate facilities for rest, sleep, meal breaks and onsite accommodation (if appropriate); and
- provide and maintain a workplace which is well lit, safe, and secure.
Providing information and training to workers about the factors that can contribute to fatigue and the risks associated with it will help them to not only do their job, but also implement control measures to minimise the risk of fatigue in the workplace.
+ Slips, trips, and falls
Slips, trips, and falls are a significant problem affecting every workplace. Slips and trips account for about 20 per cent of all lost time injuries every year across all industries. They can result in serious injuries and lengthy periods of time off work.
A slip occurs when there is insufficient friction between floor surface and footwear. Slippery floor surfaces, contaminated floors and inappropriate footwear are risk factor that can lead to slips in the workplace.
A trip occurs when there is excessive friction between a surface and footwear and/or the person’s foot is caught by an obstruction while moving. Trips can also occur when unexpected surface variations are encountered.
A fall may occur as a result of many incidents. A fall can occur when an individual is not able to correct their upright posture after they have tripped, slipped or loss their balance some other way. A fall can also occur because the surface that a person is standing on or stepping onto collapses or moves. Falls may occur from a height or on the same level.
PCBUS
Employers are required to provide information, instruction, training (e.g., risk management of slips and trips) and supervision to their employees so that they are not exposed to slips and trips hazards.
Slips and trips hazards should be controlled so far as is practicable by providing and maintaining workplaces so that workers are not exposed to slips and trips hazards.
Common risk factor categories include:
- floor surface and condition;
- floor contamination;
- objects on the floor;
- ability to see floor / walkways / hazards;
- cleaning / spill containment;
- space and design;
- stairs and stepladders;
- work activities, pace, and processes; and
- footwear and clothing.
RISK ASSESSMENT AND ELIMINATION
Where appropriate, a risk assessment should be conducted to identify risks and the means of eliminating or reducing the threat of injury.
Some of the obvious steps that can be taken to eliminate risk are:
- keeping walkways free of obstruction;
- remove sources of spills or liquid that make surfaces slippery and unsafe;
- ensuring surface work areas have effective drainage; and
- Providing adequate space to perform tasks.
CONTROL MEASURES
Where risks cannot be eliminated, consider the following control measures to manage / reduce the risks:
- clearly mark walkways, edges of steps and any changes in floor heights or surface types;
- egress, including emergency egress from the workplace is free from obstruction;
- ensure stairs are slip-resistant, have adequate depth, well-marked edges, and railing;
- provide ramps instead of steps for surface level changes;
- implement good housekeeping practices (clean as you go, keeping access ways clear, prompt spills management, keeping floors, ramps and stairs clean and dry, regular rubbish removal and appropriate storage of equipment);
- ensure that regular floor cleaning occurs and implement systems to prevent people walking on surfaces which are still wet;
- use of signage or barricades for wet or slippery areas;
- training and supervision of staff to detect and remedy risk slip/trip factors;
- clear procedures for reporting damage to floors, surfaces, and equipment; and
- where appropriate, ensure that footwear being used by cast and crew are suitable for the working surface areas.
+ Footnotes
6 Performers have a duty to inform the production’s hair and make-up artists of all known or suspected allergies, sensitivities, communicable diseases, and skin reactions.
7 AS/NZS 1576 (set): Scaffolding includes AS/NZS 1576.1:2010: Scaffolding – General requirements; AS/NZS 1576.2:2009: Scaffolding – Couplers and accessories; AS 1576.3–2015: Prefabricated and tube-and-coupler scaffolding; AS 1576.4–1991: Scaffolding – Suspended scaffolding; AS/NZS 1576.5:1995: Scaffolding – Prefabricated splitheads and trestles; AS/NZS 1576.6:2000: Scaffolding – Metal tube-and-coupler scaffolding – Deemed to comply with AS/NZS 1576.3.
8 Definition used by Safework NSW.
9 NB: A space may become a confined one if work carried out in it could generate harmful concentrations of airborne contaminants. Confined spaces need not be physically small.